AI in Manufacturing
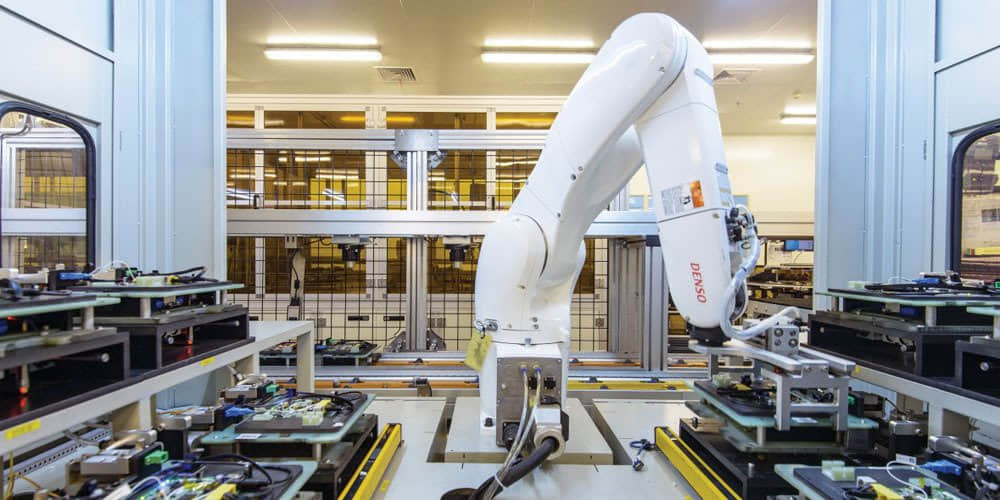
-by Junling Hu
A few years ago I attended a talk by Foxconn’s CTO. When he mentioned that Foxconn was the third largest robot manufacturer at that time, I was surprised. “In fact,” he added, “we have already built a lights-out factory.” He showed a video clip: In a factory, mobile robots moved around, robotic arms worked on components, and conveying belts were rolling smoothly. There was not a single person there. I was deeply amazed. Fast forward to today, Foxconn owns 6 lights-out factories, and more than 50,000 robots in their facilities.
Why would manufacturers like Foxconn, who is well known for its large campus of workers (more than 1 million), quest for automation? There are many reasons for such move.
Contrary to public belief that manufacturers want to exploit cheap labors, they prefer doing it without human labor. This is not just for lower cost. In manufacturing, humans are much less efficient than machines. In every step where machines replace people, the impact of worker fatigue, mistake, and body injury are eliminated. In addition, the production precision goes up. The production process can be standardized.
Mass production requires standardization. The less human in the loop, the more quality control can be achieved. Companies producing standard electronic products require high precision and quality control. This is where machine performs better than humans. In addition, the machine process is repeatable. Once programmed, a machine does not require repeated training such as those on new workers or re-training (on workers who forget the procedure). In other words, the knowledge of a machine is lifetime (for simple manufacturing procedure). Furthermore, programmed machines can be easily duplicated and expanded, assuming machine cost is relatively low.
Automation is further driven by lower machine cost and robot cost. When all the factors adding together, we will see an irreversible trend toward industrial automation.
But there are challenges in this process. Once we have machines installed in a factory and do all the jobs people used to do, the new problems arise: Machines can make a mistake, therefore they require monitoring (even though you don’t have to monitor their lack of motivation). Machine can get tired (wear and tear) and even break down. This is where monitoring, anomaly detection, and maintenance come in.
In the past, humans play the role of monitoring and control: They do visual inspection, review the data, or decide when to make maintenance. But humans are no longer to up to the task when the amount of data have increased significantly. Thousands of sensors are placed on the machine, sending real-time temperature, pressure and vibration measurement, the computing server is inundated with data coming in. In fact, for a factory with 1,000 sensors that send signals every 10 seconds, there are more than 360,000 data entries in 1 hour. In 1 day, there are more 1 million data entries. Manufacturers have entered the big data age.
For those of us who work in the Internet and mobile business, big data is already day-by-day fact we live with. When I was at eBay, we processed Terabytes of data each day. But for manufacturers, big data is a new phenomenon and something they start to grasp with. To start with, building a data infrastructure that collects, stores and processes the data is paramount.
On data collection, we will have sensors and machines that are Internet (or local network) connected. These connected devices will send information on temperature, humidity, pressure, machine condition, uptime, vibration and many more measurements to the server. The system also collects data on half-finished products, and product defects at the end of process.
On date storage, a company has to decide the location of the data: Cloud or local? This decision is linked to how much storage space we have and how much computing power is needed. Then the company has to decide on how to store the data: Putting them in a database (what kind of database) or non-database such as highly distributed file systems (say, Hadoop)? Such consideration is linked to how frequently we process the data, and how fast the response should be.
On data processing, should more data be sent to the server or be kept in the local level? This is a decision on where computing takes place. Some people advocate edge computing. Is it a fad or a trend? Once data are sent to server, we would need data engineers to clean the data and aggregate them.
Once the data infrastructure is built, we would need the next step: Making sense of data. This is where artificial intelligence becomes crucial. At the core of AI is machine learning, where the intelligent system learns from data and derives new pattern from updated data. While humans can read data, they cannot process millions of data points in a second. Machine learning can do so, and can do it repeatedly.
Therefore AI enables fast response, real-time monitoring, and predictive maintenance. For example, anomaly detection helps detecting the problem fast and continuous monitoring, thus reduces waste and disruption. An adaptive system can detect the problem earlier (say the glass bottle has a crack, and adjust the procedure). It reduces downtime and can save a lot money for the manufacturer.
Another important area is predictive maintenance. By analyzing data, we know when and how a machine will break down. Siemens has deployed a system called MindSphere that collects operating data and sensor measurements to make predictive maintenance.
AI can help improve the production process by understanding product defect happening in which stage or under what condition. The machine learning model can help us detect such pattern.
AI helps in adaptive control: Taking actions when things go wrong or situation changes. It means analyzing data and detect what causes defect, or slow down of production. It also means using data to improve efficiency.
With strong AI capability, manufacturers can save millions of dollars from machine breakdown, lost production time and delayed delivery.
Another area that needs AI is production planning. One area of AI research is planning and scheduling: How to make an intelligent agent achieve a goal by following a sequence of steps. AI scheduling is used in Kiva robots, who roam around in the warehouse in Amazon and need to coordinate their tasks. Intelligent planning is very useful for factories when they produce many parts and need to coordinate the production. A planning system can schedule each component and make them available for the next phase of production.
Finally, AI is part of robots. A robot needs computer vision, reasoning, planning, learning in addition to its grasping and moving ability. An automated factory needs robots or robotic arms that can handle complex tasks and are as dexterous as human beings.
Therefore a complete industrial AI system includes: sensor network, big data, machine learning, planning and scheduling, and robots.
Today many manufacturers are far from owning these complete capacities. Installing sensors and making machines send in data are the first step. This is why IoT (Internet of Things) becomes trendy now. The integration of adaptive system, the system that adjust its production procedure based on the component situation is still new.
Robots are not as general purpose as we hoped. Robotic hand is not as flexible as human hand. Computer vision may fail in certain cases when complex pattern appears.
There is a talent war going on between companies. Given the shortage of AI engineers and scientists, large Internet and service companies are gobbling up all the candidates they can get. This leaves few for manufacturers, whose job is not that glamourous and exciting comparing to designing apps, increase clicks or improving advertisement revenue through better targeting. How would manufacturers attract talents is a big question.
What is the future of Industrial AI? As big data infrastructure and machine learning enter mature stage now, factories embrace them to help improve efficiency and cut cost. We will see adoption of big data and machine learning approach in every factory, with all the data collected, processed and analyzed. We will see the spread of IoT in factories, growing use of robots, drones, and even speech interface with machines. AI has become an integral part of manufacturing process.
The final question is: Where do manufacture workers go? Humans are not born to do repetitive works. They lose concentration, get tired and need a break. Repetitive assembly line is not good for people in terms of their physical and emotional health. AI liberates people from such bondage, and free them to pursue jobs in service, creative arts, and computer engineering. The loss of industrial jobs is just another wave of technology migration. Similar to farm workers migrating from land to factories, we will see a wave of manufacturing workers migrate from factories to office jobs. The disappearing of manufacturing jobs heralds a new era of service industry, completing the third wave as Tofler once observed. It’s exciting to live in such an era.